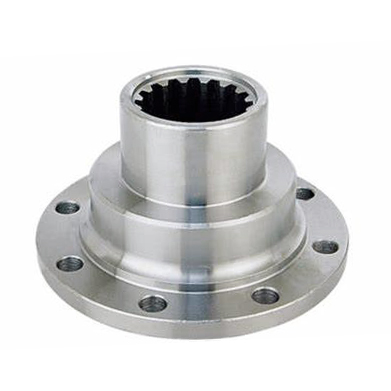
Marine Propeller Shaft
Marine Propeller Shaft
Marine propeller shafts are the main spare parts for transmitting mechanical torque, rotation, and power. Driveshafts, prop shafts, tail shafts and Cardan shafts are all names for these shafts.
Marine propeller shafts are used to transmit torque between components that are not directly connected due to distance or the need for relative motion.
Marine propeller shafts are prone to torsional or shear stress as it transmits torque. Therefore, they must be strong enough to withstand the pressure, while avoiding adding too much weight, which would increase their inertia.
3 Types of propeller shafts:
-
Tapered propeller shaft
A tapered propeller shaft is part of a wind assembly structure or tool that is attached to the propeller shaft. More precisely, it is the adjustable part of the propeller of a ship or boat that allows for changes in pitch or angle. The shaft works by utilizing a common engine design. The tapered propeller shaft is also the main connecting thread in the propeller hub. At the heart of the TPLS is a constant length helical spring that applies a constant load force.
-
Splined Propeller Shaft
These types of shafts handle torque transmission. They are the teeth of the drive shaft. Its job is to maintain alignment. Splined propeller shafts are a great way to get the most out of a marine engine. They provide better air volume with a flatter path in the engine, resulting in higher velocity ductility of the combustion air. They also help reduce vibration and unwanted noise.
-
Flanged Propeller Shaft
A flanged propeller shaft is an elongated cylindrical shaft with one or more flanges or flat circular faces at regular intervals to resist bending. Shafts of this type are commonly used in various manufacturing industries and serve different purposes.
Propeller Shafts Pictures
Marine propeller shaft materials
The material of most marine propeller shafts is mild steel. Aluminum alloys are not suitable for marine propellers because they have the fatigue limit of the rotor. When cyclic stress increases, your aluminum propeller cannot withstand this strength.
Martensitic steels are a good choice because they perform well during cyclic stress. The larger the scale they face, the more capable they are. Most commercial marine and aerospace machining uses Tobin’s bronze or Monel for their propellers because they are primarily non-corrosive. This will ensure zero or minimal leakage.
Components of Propeller Shafts
The marine propeller shaft is divided into three major components:
- Thrust shaft,
- intermediate shaft(s)
- tail shaft
The thrust shaft is the main shaft extending out of the engine. It receives rotational motion directly from the crankshaft and rotates at maximum speed in high-speed engines.
For high-revving engines, the thrust shaft is further connected to other components located further aft.
The next component is the intermediate shaft. There is no specific restriction on the number of intermediary shafts that a ship can have. However, beyond 2 shafts, it’s difficult to service and maintain. The reason for this is the large catenary force acting on the entire propeller shaft. This force deforms and damages parts because of their weight.
When coupled with the large vibrational shocks that act on the shafts, there could be permanent damage to the propeller shafts. Thus, a low number of intermediary shafts is preferred. The only reason to have multiple intermediary shafts is if the engines are far away from the propellers.
The last part is the tail shaft. It is directly connected to the propellers and lies mainly encased in the stern tube. The tail shaft is connected to the intermediate shaft by a gearbox that manipulates torque transfer. The tail shaft is built to withstand a variety of forces that may act at the stern of the ship.