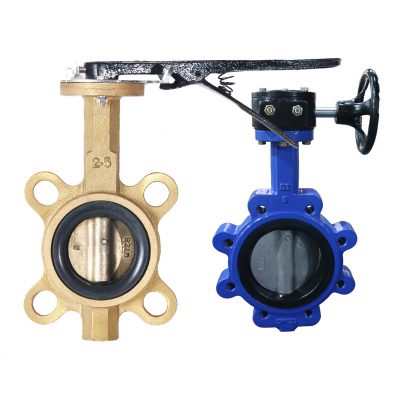
Marine Butterfly Valves
Marine Butterfly Valves
Marine Butterfly valves are the workhorse of the marine industry. These valves are easily installed and maintained. Butterfly valves get their name from the way they operate, in which vertical disc pivots to open and close around a stem, resembling the insect. Onboard ships, butterfly valves vary greatly in function and cost, from economical iron valves to triple-offset nickel-aluminum-bronze ones. Butterfly valves are “quarter-turn” valves and are traditionally operated through a lever, gear operator, or actuator. They usually come in either lugged or wafer-style bodies. The components that make up most butterfly valves are the valve body, the disc, the stem, and the seat. The seat is traditionally made of rubber and is the sealing element of the valve where it meets the disc. Seats can also be made of metal, which is common in fire-safe applications.
Marine Butterfly Valve Product Range:
- Design: JIS, DIN, API, GB
- End Connection: RF, Wafer, Lugged
- Size: 1-1/2”~48”, DN40~DN1200, 40A~1200A
- Pressure: JIS 1K~63K, 125LB~2500LB, PN10~PN420
- Material: Cast Iron, Stainless Steel, Bronze
- Operator: Lever, Gear, Pneumatic Actuator, Electric Actuator
Concentric Butterfly Valve
(Center Lined /Resilient seated Butterfly Valve)
The concentric valve is the most basic and common type of butterfly valve. This valve body connects to the disc. The connecting rod passes through the central axis of the disc. This disc is located in the center of the spool hole and the valve stem is inside the valve body.
The shift valve design is no longer known as a rubber seat valve because it relies on the flexibility of the rubber seat to block fluid flow at shut-off.
When the disc is rotated 90 degrees, it first contacts the valve stem at an angle of approximately 85 degrees. These types of butterfly valves are used for low-pressure applications.
Double Offset Butterfly Valve
(High-Performance Butterfly Valve)
For this type of HPBF valve, the disc and stem are double offset (set back behind the disc and to the side) causing the disc to rotate into place upon closure without significant seat contact. Different from a center-lined butterfly valve, the stem is located behind the disc, which enables the disc to “rub” over the seat in the last 10% of travel, during the 90-degree rotation.
This seat usually is some type of Reinforced Teflon or, for high temperatures above 230℃, the seat can be metal, usually a hardened metal, like Stellite. The most user-friendly allows removal/replacement of the stem, disc, and seat without welding.
Triple Offset Butterfly Valve
The Triple Offset Butterfly valve is designed like the double offset, but an additional third offset, which is added as the geometry of the seating surface. The seating surface creates a cone-shape of the seat and disc, which rotates into the seat with almost no contact between the sealing surfaces until it is fully closed.
This minimal contact between the disc and seat makes for an efficient sealing performance, which in turn extends the life of the valve. The seat is typically a laminated, multilayer seat sandwich comprised of a hardened material like Stellite and layers of Graphite. This design allows contact between the disc and seat only in the last 2-3 degrees.
Butterfly Valve Advantages
- Compact design; little space requirement.
- Lightweight; easily supported by the piping system.
- Less raw material and less costly.
- Quick operation; less opening or closing time.
- Easy to Install.
- Simple operation due to low operation torque.
- Available in very large sizes
- Improved energy efficiency
- Low-pressure drop and high-pressure recovery
- Long valve life
- Relatively inexpensive to build.
- Few parts; Hence, reduced maintenance.
- Butterfly valves are suitable for control purposes with linear flow characteristics between 300 and 700 of opening.
- Butterfly valve offers excellent rangeability from 30:1 to 100:1.